Bbrbet en México
Bbrbet es un sitio web de casino dirigido al mercado brasileño, lo que significa que sólo los jugadores basados en ese país pueden participar en las actividades de juego. En realidad, esto es un poco desafortunado, ya que el casino cuenta con muchas funciones estupendas.
Sitio oficial | dslauretta.com |
Año de publicación | 2019 |
Número de partidos | 2000+ |
Ofertas de bonificación | 5 ofertas promocionales que incluyen bonificación exclusiva VIP, bonificación, invitación, doble y mucho más. |
Depósito mínimo | 3 EUR |
Aplicación móvil | Android/IOS/Windows/Mac |
Entre ellas se incluyen muchas promociones únicas y útiles, un programa VIP, cientos de tragaperras, juegos con crupier en vivo, bajos requisitos de depósito y mucho más. Una de las cosas que también analizaremos es la licencia de Curaçao que tiene el casino, ya que algunos jugadores sabrán que esta autorización solía ser muy problemática.
Los mejores bonos en Bbrbet: Más oportunidades de ganar
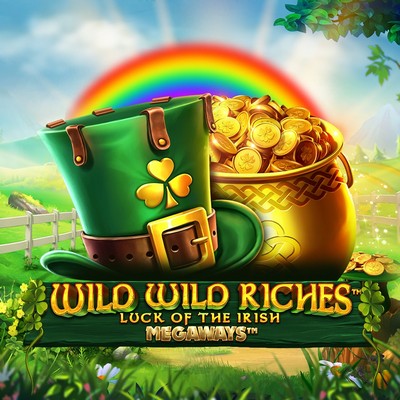
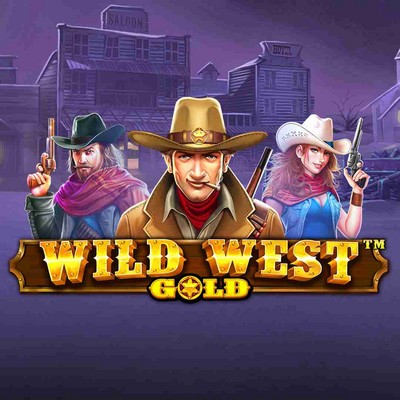
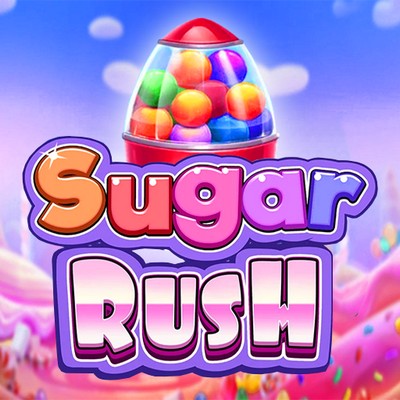
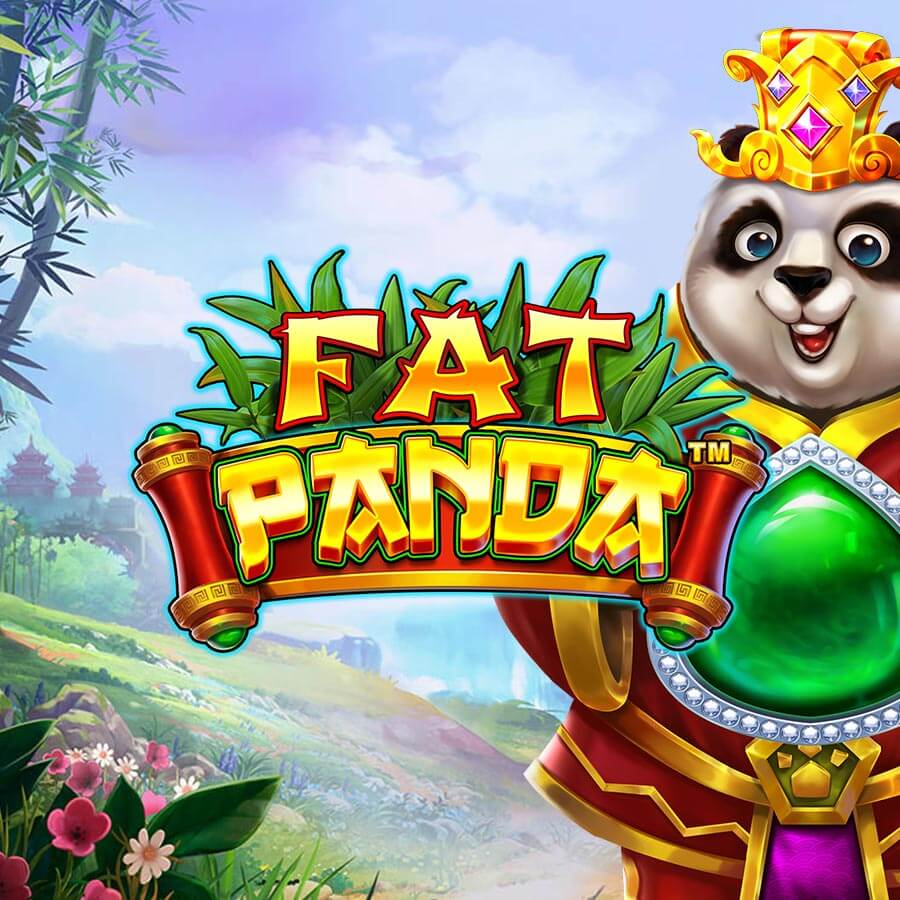
La BBRbet considera que un sistema de bonos de varios niveles, es necesario para mantener a los usuarios actuales y futuros del cliente.
En la línea actual, cuenta con 5 las ofertas de bonos destacan:
Los bonos | La información |
---|---|
Doble bonificación por invitar a tus amigos | Hace más de 3 niveles de la prima de referencia y con 2 tipos diferentes de parte de la comisión. El primero está relacionado con el número de personas a las que se les invita. Se puede llegar a ganar hasta 50 euro por cada invitado en el nivel 1st . De la misma manera, usted puede obtener una bonificación de hasta el 0,3%, en cada una de los usuarios a los que ha invitado a unirse a la RESISTENTE Bet.com. |
El bono de bienvenida | Haz un depósito de al menos 3 euro, a fin de recibir un bono del 100% hasta un máximo de 400 euro. El bono sólo puede ser utilizado una sola vez y tiene un límite máximo de pago de 30 veces el monto de la prima. |
El Programa VIP | En función de los depósitos correspondientes hecho, usted puede llegar a los 13 niveles del programa VIP. Se le anima para mejorar los límites de giro (deg), las tasas más bajas de devolución de dinero en efectivo más alto y el valor máximo de la apuesta de euros. |
Los pagos mensuales. | El BBRbet casino, que anima a los usuarios a llevar a otros usuarios, por lo que se puede llegar a ganar hasta 1 millón de euro al mes, invitando a los nuevos jugadores, y por lo que les invitamos a nuevos jugadores. |
Los bonos de la fiscalía | Los usuarios están dispuestos a monetizar su base de seguidores en las redes sociales, pueden llegar a ganar hasta 20.000 euro en comisiones diarias, por la distribución de ingresos en distintos niveles. |
Juegos de casino: Amplia selección de juegos de los principales proveedores
En Bbrbet Casino, estamos orgullosos de ofrecer a nuestros jugadores una amplia gama de juegos entre los que elegir. Entendemos que cada jugador tiene diferentes preferencias y necesidades cuando se trata de juegos de azar en línea, por lo que hemos preparado una amplia colección de juegos de los principales proveedores de juegos.
Nuestra selección incluye máquinas tragaperras clásicas y modernas, juegos de mesa, vídeo póquer y juegos con crupier en vivo, lo que garantiza que cada jugador pueda encontrar el juego perfecto que se adapte a sus intereses.
Nuestro compromiso de ofrecer una amplia gama de juegos es la razón por la que estamos seguros de que Bbrbet Casino es su camino hacia un sinfín de aventuras de juego. Únase a nosotros hoy mismo y experimente la emoción de nuestra amplia selección de juegos.
Bbrbet: Cómodos métodos de pago y soporte 24/7
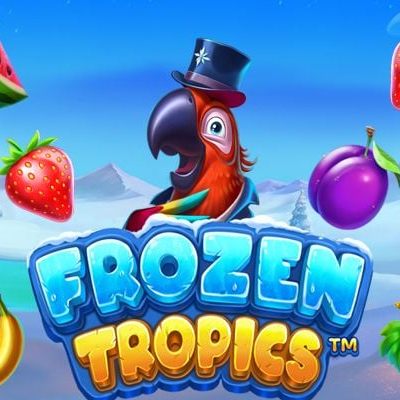
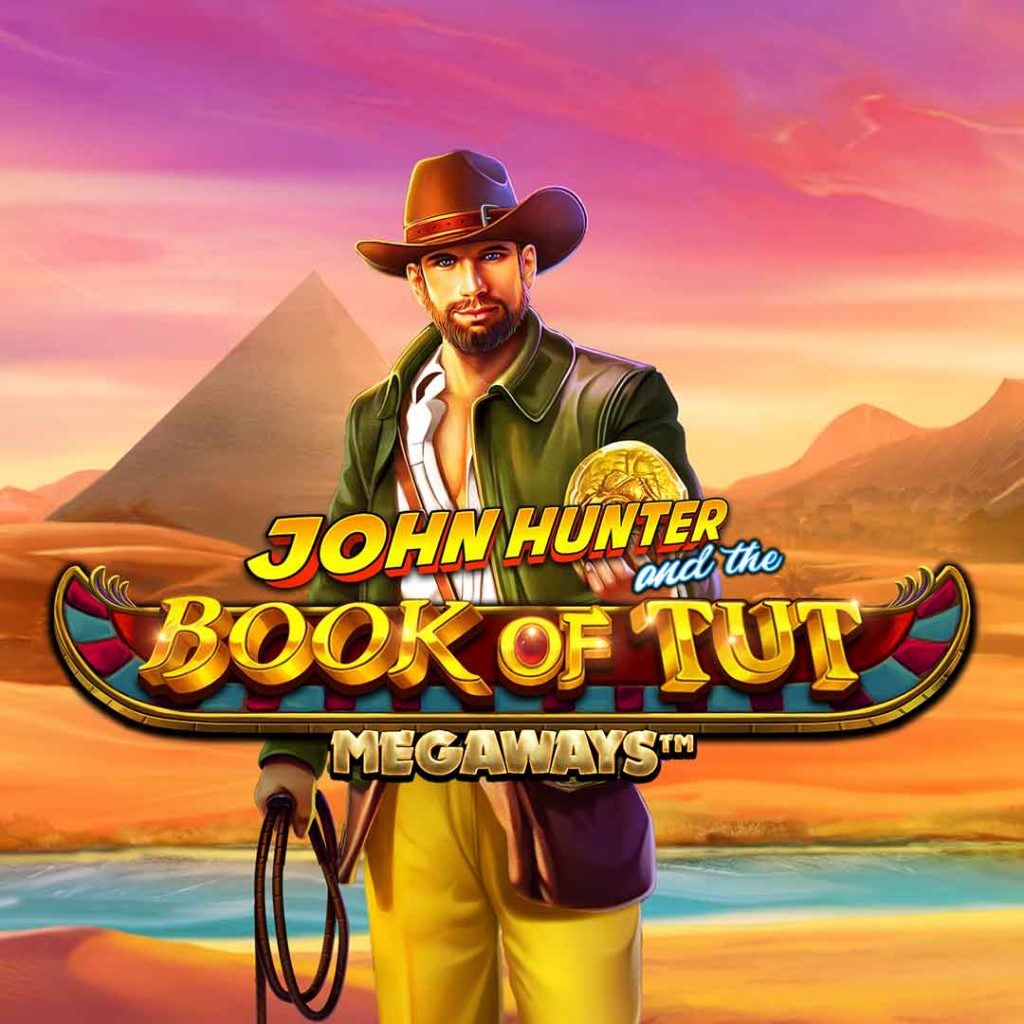
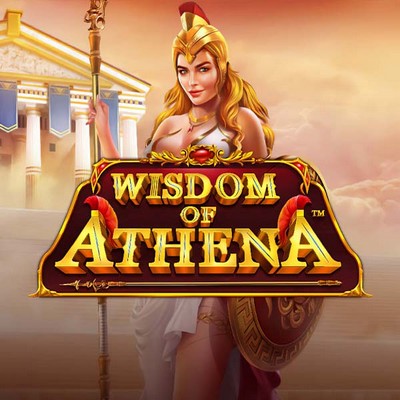
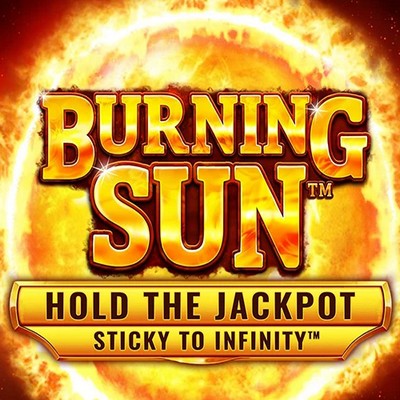
Puede consultar una lista de las opciones bancarias disponibles para los jugadores brasileños haciendo clic en el icono del monedero (rojo), en la esquina superior derecha.
Sólo hay una opción disponible para depósitos y pagos: PIX. Esto demuestra que la plataforma BBRbet se preocupa más por la seguridad y la rapidez de las transacciones, garantizando que los jugadores brasileños puedan disfrutar de pagos instantáneos.
El Sistema de pagos de | Los límites de depósito | Los límites de giro (deg) |
---|---|---|
PIX | 20(3)EUR/BRL – 100.000(19.000) EUR/BRL | 50(9) EUR/BRL – 10.000(1800) EUR/BRL |
Para ayudar al usuario es muy importante cuando se juega juegos de casino o cuando se utiliza la plataforma de juegos de azar, para cualquier otro propósito.
Este sitio web puede ofrecer una gran experiencia en todas las plataformas, con representantes experimentados, sensibles y que hablan portugués, disponible las 24 horas del día, 7 días a la semana.